We just received pictures from BAC of the seat insert that was made for me. Merry Xmas from BAC! This polystyrene bead seat insert was originally formed to my backside by Pro-Seat (see our post: HERE) during one of my visits to jolly ole England. BAC have finalized the trim and it turned out beautifully. Truly a first class insert! This will be available as an option for those would need a bit more support or adjustment for height and reach. See the pictures below:
Related to this, a larger seat is also in the works. See the picture below and note the red arrows that show the rough amount of additional width that can be realized by reshaping the carbon fiber seat. This will be very welcome for those with wider than average hips.
Monday, December 24, 2012
Wednesday, December 12, 2012
Mono Build Entry #17 - Winglets
0007 now has wings. Using full scale templates from the CAD data for the car, we mounted the front winglets to the core body panels. The winglets came late in the development of the Mono, and stemmed from the CFD work done on the car by Stuttgart University. While at first glance they might seem purely for down force, the winglets main function is to clean and direct the air flow to the radiators.
Saturday, December 8, 2012
Pro-Seat Insert Fabrication for Sportscars
Alex Powell from Pro-Seat in the UK has been with us for the last two weeks training us in the art of producing custom seat inserts for sportscars. These inserts are designed to hold the driver properly in his/her seat, so that they do not move while driving under load. This has been a challenge for me in almost every car I've put on track. I'm constantly fighting g-forces and sliding around in my seat.
Alex's father, Trevor, invented this FIA-approved bead-based seat insert in 1992. I met these two gents back in March through our partnership with BAC. Pro-Seat have supplied all levels of motorsport including F1, CART, WRC, LMP and much much more. Many famous racers have been well fitted and protected by a Pro-Seat insert.
Alex began our lesson by showing us the process of 'dry-fitting' a seat. This is done with the bag of polystyrene beads by approximating the amount of material required by the driver. A vacuum is pulled on the bag, the insert is installed and the driver put in place. We used an Atom3 in this example - I've been tired of being thrown around in the stock Atom seat!
With the driver in place, the beads are sculpted around the body and fill in any gaps between the body and the seat. Driver seat height is checked to ensure he/she is sitting high or low enough. To be clear, the Pro-Seat insert does need a 'shell' to be molded into to provide it structure. It is not a stand alone seat. We use the Atom3 stock seat as our 'shell' for this insert.
The driver is carefully extracted from the insert and a rough insert remains. See it below. This is used as a reference to determine where the beads need to be placed on the final insert formation.
Trevor is shown below, pouring a two-part resin into the bead bag. This resin is a glue that holds the beads together and allows them to form to the drivers body and maintain its shape.
Though this insert is a natural product for formula style cars, like the Atom or BAC Mono, it can also be used in traditional race seats. We produced one for a gentleman with a Recaro ProRacer HANS seat as shown. See the inserts below.
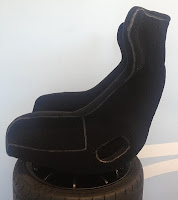
John races his BMW 3series in SCCA and has found the seat to be uncomfortable as he has some hip pain from a previous accident. We removed the seat padding and fit him with an insert. We think that even clients with traditional race seats can benefit from a Pro-Seat insert. So expect to hear about us offering this product and service for all sportscars in the very near future.
![]() |
Note the F1 driver on the screen? |
Alex began our lesson by showing us the process of 'dry-fitting' a seat. This is done with the bag of polystyrene beads by approximating the amount of material required by the driver. A vacuum is pulled on the bag, the insert is installed and the driver put in place. We used an Atom3 in this example - I've been tired of being thrown around in the stock Atom seat!
With the driver in place, the beads are sculpted around the body and fill in any gaps between the body and the seat. Driver seat height is checked to ensure he/she is sitting high or low enough. To be clear, the Pro-Seat insert does need a 'shell' to be molded into to provide it structure. It is not a stand alone seat. We use the Atom3 stock seat as our 'shell' for this insert.
The driver is carefully extracted from the insert and a rough insert remains. See it below. This is used as a reference to determine where the beads need to be placed on the final insert formation.
Trevor is shown below, pouring a two-part resin into the bead bag. This resin is a glue that holds the beads together and allows them to form to the drivers body and maintain its shape.
When the resin is added, you have approximately 3 hours to form the final insert. The beads take on a doughy consistency so it becomes quite easy to form and shape. The 3 hour window gives the insert maker, enough time to sculpt his masterpiece.The rough insert still has the plastic covering that will be trimmed off along with the excess polystrene beads. This rough insert still needs to cure for 12 hours before we can begin our trimming process.
The next stage of the insert construction will remove the excess parts. First rough cuts are made and then finer and finer shaping cuts are used to create the insert. Holes are cut out for waist and anti-sub belts. The insert is then sanded to give a smooth surface for the fire-retardant upholstery.
The final insert is shown below in an Atom3. These inserts are seat and driver specific - unless of course you have an identical twin. An interesting characteristic of the beads used in this insert, is their ability to sustain some deformation yet still recover its original shape. Pro-Seat often cite the example of Mark Blundell crashing his Indy car in 1997 at Homestead Spring testing. This crash destroyed his car but the insert was still useable for the remainder of the season. Not that I plan to experience this benefit, but I am sure glad that the insert offers that level of protection.Though this insert is a natural product for formula style cars, like the Atom or BAC Mono, it can also be used in traditional race seats. We produced one for a gentleman with a Recaro ProRacer HANS seat as shown. See the inserts below.
![]() |
Recaro ProRacer |
![]() |
Insert for Recaro ProRacer |
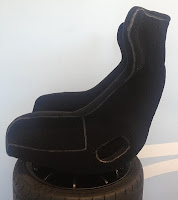
John races his BMW 3series in SCCA and has found the seat to be uncomfortable as he has some hip pain from a previous accident. We removed the seat padding and fit him with an insert. We think that even clients with traditional race seats can benefit from a Pro-Seat insert. So expect to hear about us offering this product and service for all sportscars in the very near future.
Friday, December 7, 2012
Mono Build Entry #16 - Rear Diffusers and Wishbones
For our Friday edition of the Mono build entry, we will start with a totally random, cool picture of 0007:
With the diffusers in place, we are also working to assemble the rear suspension. The wishbones are now in place, with the axles and uprights still to go.
Circling back to the current status of the build, we have now finished the fitment of the rear diffuser panels. As you can see, the official name of these panels doesn't quite do them justice, as they are not only diffusers for the car, but a continuation of the core body panels and also rear wheel arches as well.
0007 with rear diffusers in place |
Looking from the right rear wheel arch towards the center line of the car. Note the spherical bearings all contain special lip seals to keep out dirt and grit. |
Rear View, with the right side having the stays and wishbones in place and the left with only wishbones attached. |
Tuesday, December 4, 2012
Mono Build Entry # 15 - Front Suspension
Continuing with the Mono build, we have completed the initial construction of the front suspension. These parts are a fairly easy assembly, with the main concern being to not scratch the core body panels!
The Right Front Suspension: Fabricated aero tube upper and lower control arms, billet upright and rocker, track rod and anti roll bar link, Sachs Damper. |
Left Front Suspension. |
Low Angle of Right Front Suspension. |
Friday, November 30, 2012
Mono Build Entry #14 - Radiators
0007 now has the last of her cooling system in place, with both radiators being mounted. In keeping with the overall quality of hardware on the Mono, the radiators are lovely items. Tapered and fully TIG welded with bespoke light weight mounting brackets, it's a shame they are eventually covered with the side pods!
Left side, front view. |
Left side, rear view. |
Right side radiator in the back ground, initial layout of some of the suspension in the foreground. |
Right side, front view. |
Tuesday, November 27, 2012
Mono Build Entry #13 - Plumbing Details
In preparing the Mono for it's first run test, we have been in the throes of taking care of the last bits of plumbing on the car. One interesting bit on the Mono is the engine oil tank is incorporated into the casting for the transmission, just behind the bellhousing interface.
In the same fashion, the catch tank for the car is cast into the bellhousing. The picture below shows the left side plumbing details.
As you can see in these pictures, this car is packaged pretty tightly, and we have to put a lot of care into making sure the routing of the lines and orientation of the fittings are correct. Next up are the radiators, and with a few wiring details sorted, we will be ready for our first run test.
Tuesday, November 20, 2012
Mono Build Entry #12 - Core Body Panels
Currently at Sector 111 we are fitting the first body panels on the Mono, which we call the "Core" body panels. As their name suggests, the core body panels provide the base for all of the other body work and fairings, essentially wrapping the center section of the chassis, and extending down over the top side of the Jabroc floor.
In the picture below you can see mounts for the front suspension and steering protruding from the holes in the body work. All suspension and running gear must go on after these panels are installed.
As with all the body panels on the Mono, the Core Body panels are made entirely from carbon fiber. The next picture shows the chassis on the jig, with the core body panels loosely in place.
There are several bespoke fastener solutions found on the body work for the Mono, such as the M5 Buttons which hold the Core Panels to the floor. These machined pieces are an excellent example of the attention to detail that go into the Mono: Not only do they provide increased contact surface area when compared to a traditional fastener, but when the other panels are installed you can hardly notice them, giving a seamless, integrated look the the body.
Friday, November 16, 2012
Mono Build Entry #11 - Intake Notes
One interesting, and certainly "Tasty Bit" of the Mono lies in the Cosworth F1 style throttle body. Instead of normal throttle butterflies, the cast / CNC machined intake features a rotating internal cylinder. The cylinder has openings for all four intake ports, and the size of the aperture leading to each cylinder is dependent on the position of the barrel. At wide open throttle, there are no butterflies to restrict the intake flow.
Idle
Half Throttle
Wide Open - Note the tapering, nearly straight intake tract and hand finished porting in the cylinder head! All very nice features, and a true mark of Cosworth quality.
Wednesday, November 14, 2012
Mono Build Entry #10 - Chassis to Jig
With the majority of the components fixed to the center portion of the chassis, it became time to set 0007 on her floor!
The floor of the Mono is constructed of 3 separate pieces of 5mm thick "Jabroc". Jabroc is a high density wooden laminate. This gives the material excellent wear characteristics when used as a skid plate, and is used across all forms of motorsport, including F2, F3, LMS, ALMS, etc.
The three sections of floor are machined in order to overlap at the joints, and all fastener holes are countersunk to keep the bottom of the floor perfectly flat. Stainless hardware is used to secure the Jabroc to the captive fasteners attached to the aluminum sub-floor.
The floor of the Mono is constructed of 3 separate pieces of 5mm thick "Jabroc". Jabroc is a high density wooden laminate. This gives the material excellent wear characteristics when used as a skid plate, and is used across all forms of motorsport, including F2, F3, LMS, ALMS, etc.
The three sections of floor are machined in order to overlap at the joints, and all fastener holes are countersunk to keep the bottom of the floor perfectly flat. Stainless hardware is used to secure the Jabroc to the captive fasteners attached to the aluminum sub-floor.
The joining of the chassis to the floor went very smoothly. Only a few fore/aft and lateral adjustments were required to get all the bolts in, and have the car centered on the jig. With this process complete, we can now turn to one of the more difficult aspects of the Mono, which is fitting the body work...
Subscribe to:
Posts (Atom)