Keeping your wheels attached to your car is critically important. The most obvious opening statement for a blog post ever, I know. However, I do believe that familiarity breeds contempt and the little studs (or bolts) that hold your wheels to your ride do not get enough respect. The torque spec that your manufacture recommends is actually pretty important when it comes to wheel bolts and studs. There are times where "good and tight" is acceptable, your wheels are not one of those times.
As discussed all across the internet (including in this
BLOG), and in fine books and pamphlets all over, fastener torque is critical to the strength of any joint. Also, the torque applied to a bolt is not the critical bit. What is critical is the amount a bolt is stretched (stained) when it is installed (ever wonder why rod bolts in an engine are not just torqued, but measured?). A torque value is just a handy way to measure and apply a set amount of strain. The torque value for a fastener is calculated by estimating things like the friction factor between the fastener and its mating part, or experimentally where strain is measured for a specific application and the torque required is noted.
When working on cars here, we often see studs that have obviously not been properly torqued. Usually this means they are WAY too tight and this happens for 3 main reasons:
- Use of an impact gun
- Torquing hot wheels
- Stud lubrication
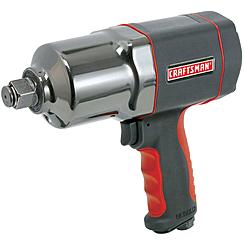 |
Leave this tool in your box
when working on your sports car. |
1. Impact Gun
The first most common mistake is that people put wheels on with an impact gun, this crime is committed most often (oddly enough) by wheel/tire shops. You would think that people that specialize in putting wheels on cars would do the task correctly, but they do not. It is such common practice to just buzz the lug nuts/studs/whatever on that no one bats an eye. If you are using an impact gun, how do you know that the torque is correct? Too much torque puts too much strain on the stud and the wheel itself, worst case, the stud snaps. Too little torque actually puts too much strain on the stud as well and severely lowers its fatigue life. Worst case, stud snaps. Nothing good has ever happened after a wheel stud failure. We NEVER use an impact to install wheels here. We also never use one to remove wheels either. Using an impact is hard on the wheel lugs/nuts and doing it by hand with a breaker bar allows you to feel if something is not right (over/under torqued, bad threads, etc.)
2. Torquing Hot Wheels
The second most common offense? The habit of torquing wheels right after a track session. In this scenario, the wheel studs and everything else associated with the hub are pretty hot, hot enough to change the strain in the system. So sometimes you can turn the bolt a little bit farther with the same amount of torque. You have now tightened the bolt further than you did initially (when it was cold), and now when everything cools back down, the bolt is strained more that originally intended. We think that this is minor but we still never recommend torquing hot wheels.
For peace of mind, you can check for loose bolts but wait till the wheels have cooled before checking torque. Do it just before your session starts.
3. Stud Lubrication
The third reason why wheel bolts get over torqued is lubrication of wheel studs. As mentioned early, the torque applied to a threaded fastener is meant to produce an ideal amount of pre-stress or strain in the fastener. Most of the force (torque) applied to a fastener (about 90%) while you were tightening it is not stretching the bolt, it is overcoming the friction between the two mating threads as well as the friction generated under the head of the bolt. So then the amount of friction between the parts is critical in determining the correct torque to produce a given strain. The friction can vary wildly depending on the bolt plating, thread class, materials, and lubrication. Most torque values given by manufactures are for dry threads unless stated otherwise. So if you have a torque spec for a dry thread, then you lube it with something like anti-seize or thread locker, you are going to reduce the friction and you will end up with much more strain in the fastener for the same amount of torque applied.
If a fastener does not call for lubrication, it is usually best not to lube it.
So if all these mistakes are being made and people are over torquing the hell out of wheels all the time, why aren't wheels flying off cars and people dying in fiery crashes 24/7? Safety factors. Engineers always design things with a safety factor and make things able to withstand loads usually 2-10 times higher than what is expected (air craft and race car engineers usually use safety factors under 2 to reduce weight). This covers things like over torquing, misuses, accidents, etc. However, the wise (wo)man respects the safety factor she is given and does not try to push his luck. Wheel studs CAN and DO fail from improper torque.
We Recommend:
1)Torque your studs/bolts/lug nuts with a torque wrench and according to the manufacture's specifications.
2)Tighten your lug nuts in a criss-cross or star pattern for even torque with a torque wrench
3)Check your wheel torque at least twice a day at the track - when the wheels are cold. We like to check before every session.
4)Use a torque wrench (was repetitive enough?)