One of the great advantages of an Ariel Atom is that the mild steel chassis can easily be repaired. We recently fixed an Atom that suffered chassis damaged at a suspension (wishbone) mount. The guys stripped down the chassis to improve access to the bent part. They then cut out the bent part. A new section was positioned with clamps and measurements were taken to ensure the position was correct. They then welded in the new section. It was masked off and spray painted to match. The parts were reinstalled and the car was aligned. Quick and easy!
Wednesday, March 13, 2013
Wednesday, March 6, 2013
Mono Blog Entry #21: Shakedown & Troubleshooting
The first Mono built by us has effectively been a 'test mule'. This car allowed us to learn how to build the car, troubleshoot it, and ensure it is fit for use in North America. Additionally we have been writing the build manual so documenting the process has shed light on various areas that need to be addressed with more detail. Even with 13 man weeks of training at the BAC factory, we have learned even more by building this first car.
So what have we learned so far? We would like to believe that assembling a car would go without issue, but experienced people recognize that this is not generally the case. Ian and Neill Briggs, from BAC, visited us a week ago to evaluate this first car and provide us additional insights. Even with the daily emails/phone calls that we've had with the engineering and operations staff back in Homes Chapel, a face to face meeting is always benefitial. So here are some of the items that we experienced and our corrective actions.
Inoperative Fuel Gauge: We calibrated the fuel gauge on the Mono but it only showed a full tank of fuel and did not change regardless of tank level. Corrective Action: The steering wheel needed to be updated with a hardware change to match the current fuel level sending unit. The factory has inspected their stock and confirmed that future wheels are correct.
Gear Fluid Leak #1: We found fluid leaking from the left side gearbox drive flange of the car during the initial test drive. We thought the seal might be bad, but it turns out the circlip that holds the flange in place was missing. Hewland does not ship this gearbox to F3 teams with this circlip - these teams have another retention system. The Mono spec requires it, so we installed them on both sides and the leak was fixed. Corrective Action: Hewland spec has been corrected at the factory and all future gearboxes will be inspected for circlips.
Gear Fluid Leak #2: Fluid was leaking from the rear gear position sensor plate. This adapter plate allows us to get the proper gear reading on the steering wheel by positioning the mechanical sensor. Corrective Action: We've added a small amount of sealant to the plate to correct the leak. The installation instructions have been updated to reflect this addition.
Engine oil leak: We had a minor oil leak from the oil pressure sensor fitting. The fitting we had received was the wrong type and it did not seal correctly. Corrective Action: Specification has been updated and build manual adjusted to reflect the correct type of fitting
Coolant Leaks: We've had a few coolant leaks that have come from various hoses. Corrective Action: Tightening the clamps have corrected the problem. Procedure has been changed to re-tighten hose clamps after the first full warm up of the car.
Body gaps: The entire Mono body is hand fit. This takes a fair amount of time to get the panel gaps correct. This attention to detail is what differentiates the Mono from other low production vehicles. With input from BAC, during their visit, we've learned some additional tricks to get the gaps very consistent.
Loose Fuel Tank Internal Clamp: The hose that connects to the high pressure side of the internal fuel pump popped loose and stalled the car. The Oettinger clamp, used on this hose, was not crimped tight enough. Corrective Action: We inspected all tanks in stock and BAC are working with the tank supplier to correct this issue. We've recommended a change of clamp type to improve the quality of the connection. This is now under discussion.
Inoperative Lambda Sensor: During start-up we noticed our AFR readings were not working on our laptop review of live car data. We traced the problem to a connector that was pinned incorrectly. Corrective Action: We swapped the unit out initially to fix it quickly. The bad unit is getting repinned and future units will be inspected for correct pin-outs. The factory is correcting their procedures to reflect this issue.
Stone Damage: Within 20 miles of driving, the rear fenders of the Mono began seeing serious stone impingement. We brought the car over to our Clearbra specialist, ClearPro to have her protected. After another 500 miles of driving the car revealed additional areas that also need to be covered. Corrective Action: Increase coverage area to clear bra kits and look at thicker materials to provide better protection in the most vulnerable areas.
The learning curve has been steep for us, but this has also been a significant benefit for BAC as we act as an extension of their factory. Several items that we've shed light onto have helped our friends at BAC to improve the build of the Mono. This first car has delivered enough clarity that the subsequent cars will be built faster and to an even better standard. A custom built, low-volume car requires patience and we have been getting pretty good at taking the proper perspective.
So what have we learned so far? We would like to believe that assembling a car would go without issue, but experienced people recognize that this is not generally the case. Ian and Neill Briggs, from BAC, visited us a week ago to evaluate this first car and provide us additional insights. Even with the daily emails/phone calls that we've had with the engineering and operations staff back in Homes Chapel, a face to face meeting is always benefitial. So here are some of the items that we experienced and our corrective actions.
![]() |
I had to stop and take a picture of the odometer |
Gear Fluid Leak #1: We found fluid leaking from the left side gearbox drive flange of the car during the initial test drive. We thought the seal might be bad, but it turns out the circlip that holds the flange in place was missing. Hewland does not ship this gearbox to F3 teams with this circlip - these teams have another retention system. The Mono spec requires it, so we installed them on both sides and the leak was fixed. Corrective Action: Hewland spec has been corrected at the factory and all future gearboxes will be inspected for circlips.
Gear Fluid Leak #2: Fluid was leaking from the rear gear position sensor plate. This adapter plate allows us to get the proper gear reading on the steering wheel by positioning the mechanical sensor. Corrective Action: We've added a small amount of sealant to the plate to correct the leak. The installation instructions have been updated to reflect this addition.
Engine oil leak: We had a minor oil leak from the oil pressure sensor fitting. The fitting we had received was the wrong type and it did not seal correctly. Corrective Action: Specification has been updated and build manual adjusted to reflect the correct type of fitting
Coolant Leaks: We've had a few coolant leaks that have come from various hoses. Corrective Action: Tightening the clamps have corrected the problem. Procedure has been changed to re-tighten hose clamps after the first full warm up of the car.
Body gaps: The entire Mono body is hand fit. This takes a fair amount of time to get the panel gaps correct. This attention to detail is what differentiates the Mono from other low production vehicles. With input from BAC, during their visit, we've learned some additional tricks to get the gaps very consistent.
Loose Fuel Tank Internal Clamp: The hose that connects to the high pressure side of the internal fuel pump popped loose and stalled the car. The Oettinger clamp, used on this hose, was not crimped tight enough. Corrective Action: We inspected all tanks in stock and BAC are working with the tank supplier to correct this issue. We've recommended a change of clamp type to improve the quality of the connection. This is now under discussion.
Inoperative Lambda Sensor: During start-up we noticed our AFR readings were not working on our laptop review of live car data. We traced the problem to a connector that was pinned incorrectly. Corrective Action: We swapped the unit out initially to fix it quickly. The bad unit is getting repinned and future units will be inspected for correct pin-outs. The factory is correcting their procedures to reflect this issue.
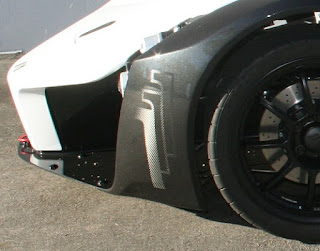
The learning curve has been steep for us, but this has also been a significant benefit for BAC as we act as an extension of their factory. Several items that we've shed light onto have helped our friends at BAC to improve the build of the Mono. This first car has delivered enough clarity that the subsequent cars will be built faster and to an even better standard. A custom built, low-volume car requires patience and we have been getting pretty good at taking the proper perspective.
Subscribe to:
Posts (Atom)